Bolsters
Bolsters are the interface between the forging press and the die. They have to meet the following requirements::
Some of the above requirements are in direct conflict, and via close communication with the customer the optimum must be found. We are literally the interface between the forger and the press manufacturer.
Another frequent field of activity is the retrofit of presses that were bought secondhand, to make them fit for their new use. The challenge lies to find the optimum configuration with the given geometry of the press and the existing ejectors.
With our experience we support the customers in the design of the press bolsters. Over a period of more than 30 years many different types of clamping, guiding and die-change systems have been designed and supplied. About 700 bolsters for a wide range of press types, brands and sizes (4,000 kN to 80,000 kN) have been delivered to customers in Italy, Germany, Poland, India, Korea, USA, Mexico, etc.
- Shortest possible time to change the dies, tool set-up not affecting production
- Rigidity to withstand high mechanical loads
- Ruggedness to withstand excessive dirt, scale, graphite, etc.
- Resistant against aggressive die lubricants
- Reducing the mismatch caused by the necessary clearance in the ram guides
- Mismatch correction in X and Y direction
- Heating of the dies up to 300°C
- Keeping forging accuracy at varying temperatures
- Clamping of current dies, legacy dies, dies from other presses (interoperability)
- Possibility of my combinations for the ejectors
Some of the above requirements are in direct conflict, and via close communication with the customer the optimum must be found. We are literally the interface between the forger and the press manufacturer.
Another frequent field of activity is the retrofit of presses that were bought secondhand, to make them fit for their new use. The challenge lies to find the optimum configuration with the given geometry of the press and the existing ejectors.
With our experience we support the customers in the design of the press bolsters. Over a period of more than 30 years many different types of clamping, guiding and die-change systems have been designed and supplied. About 700 bolsters for a wide range of press types, brands and sizes (4,000 kN to 80,000 kN) have been delivered to customers in Italy, Germany, Poland, India, Korea, USA, Mexico, etc.
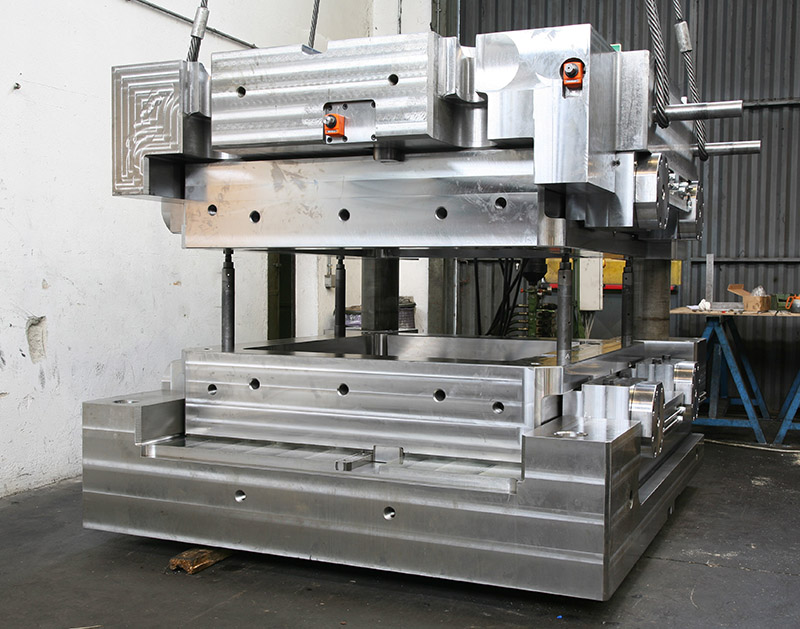

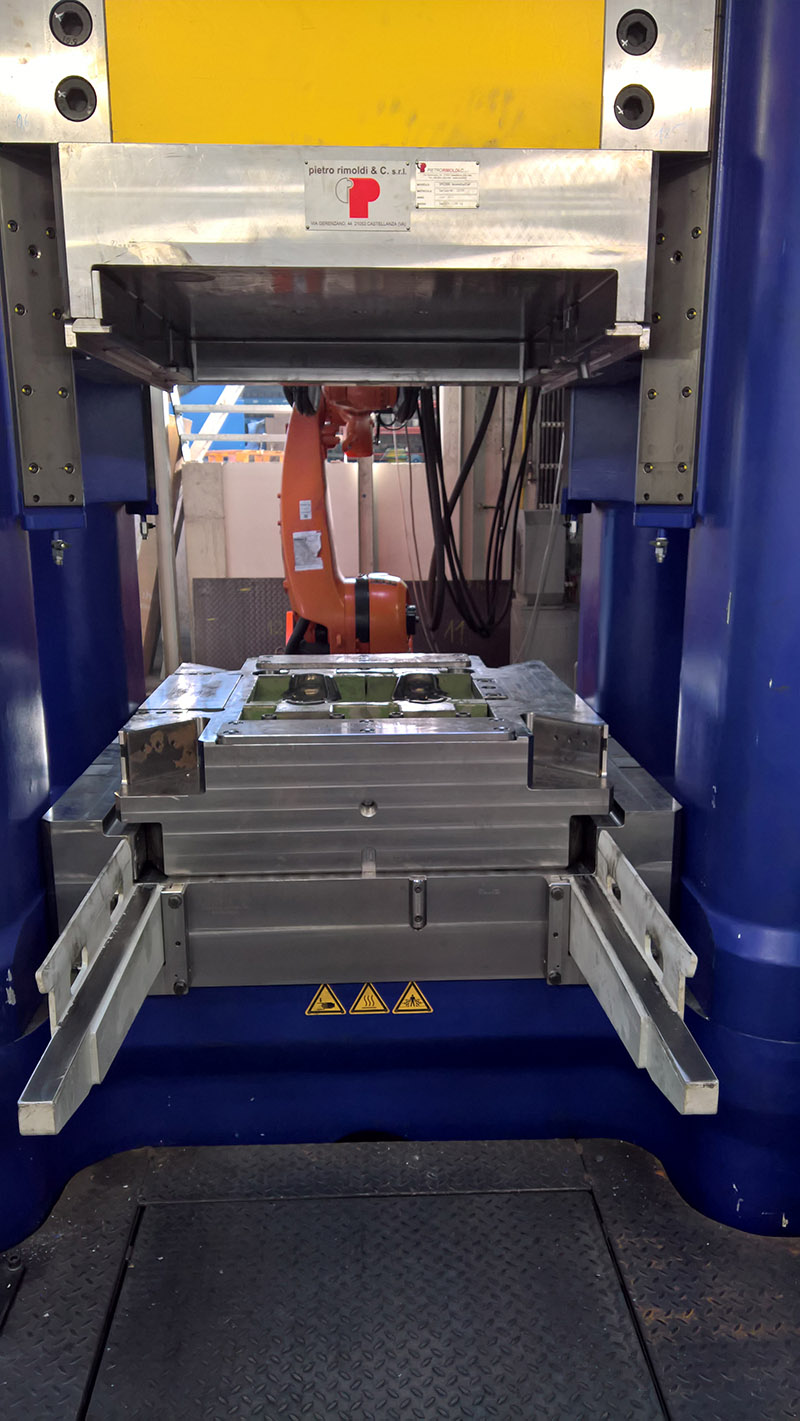
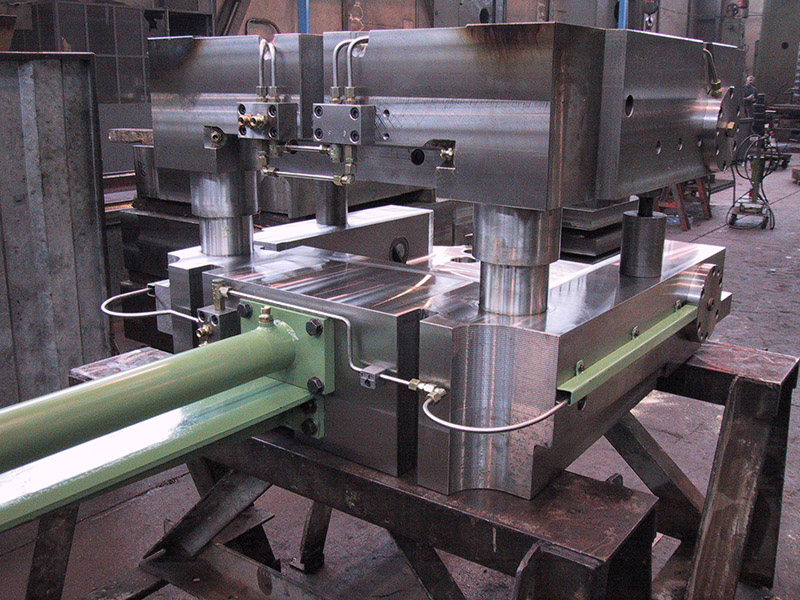
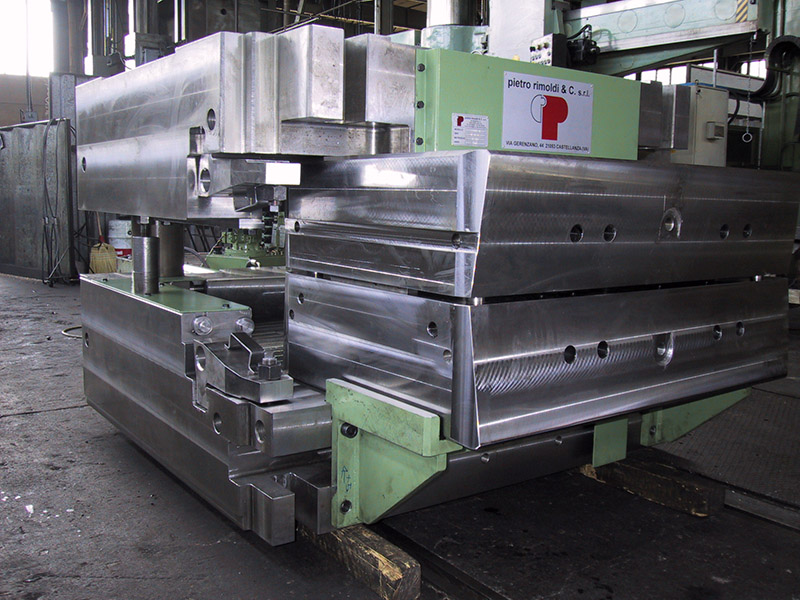
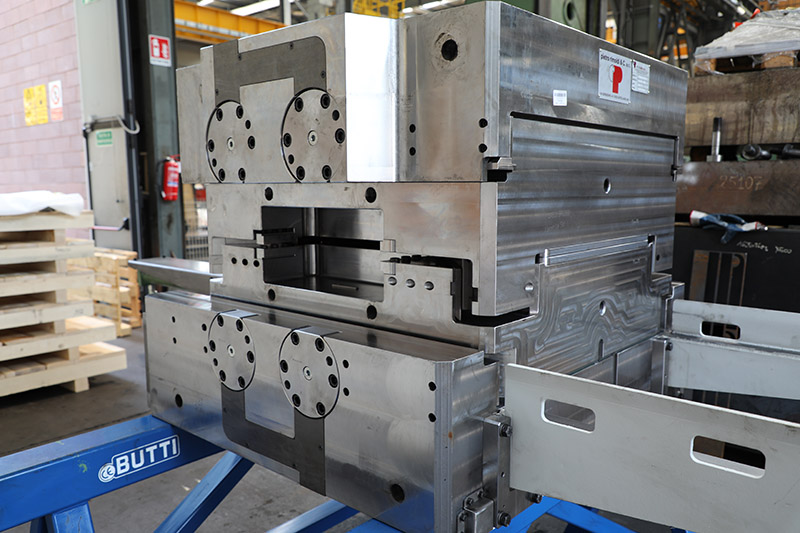
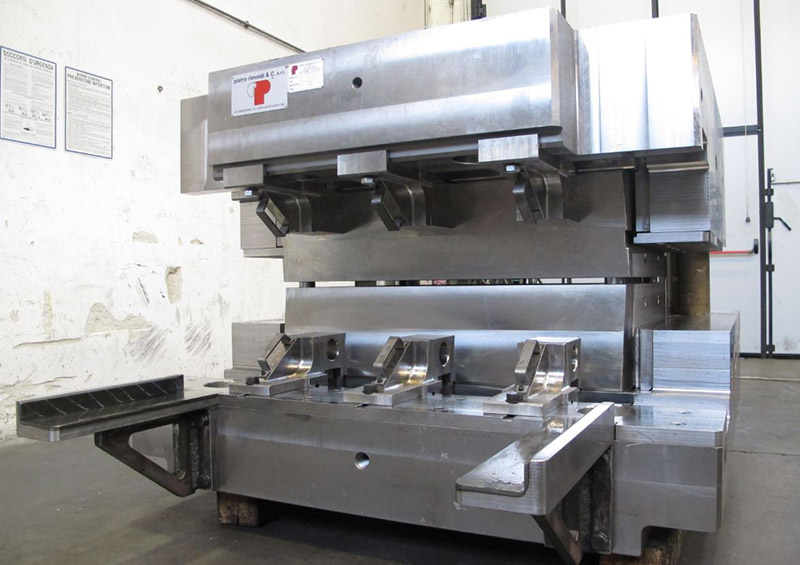
